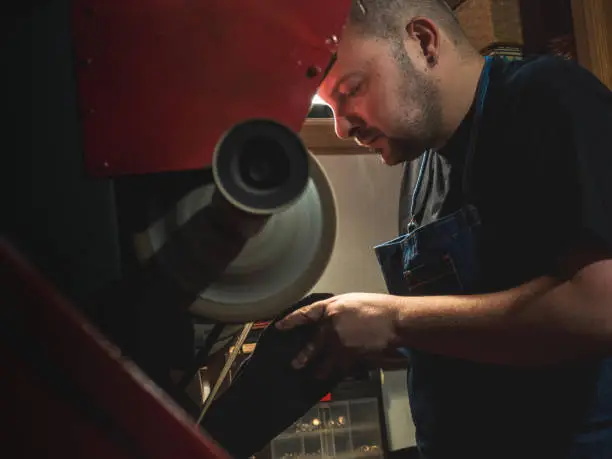
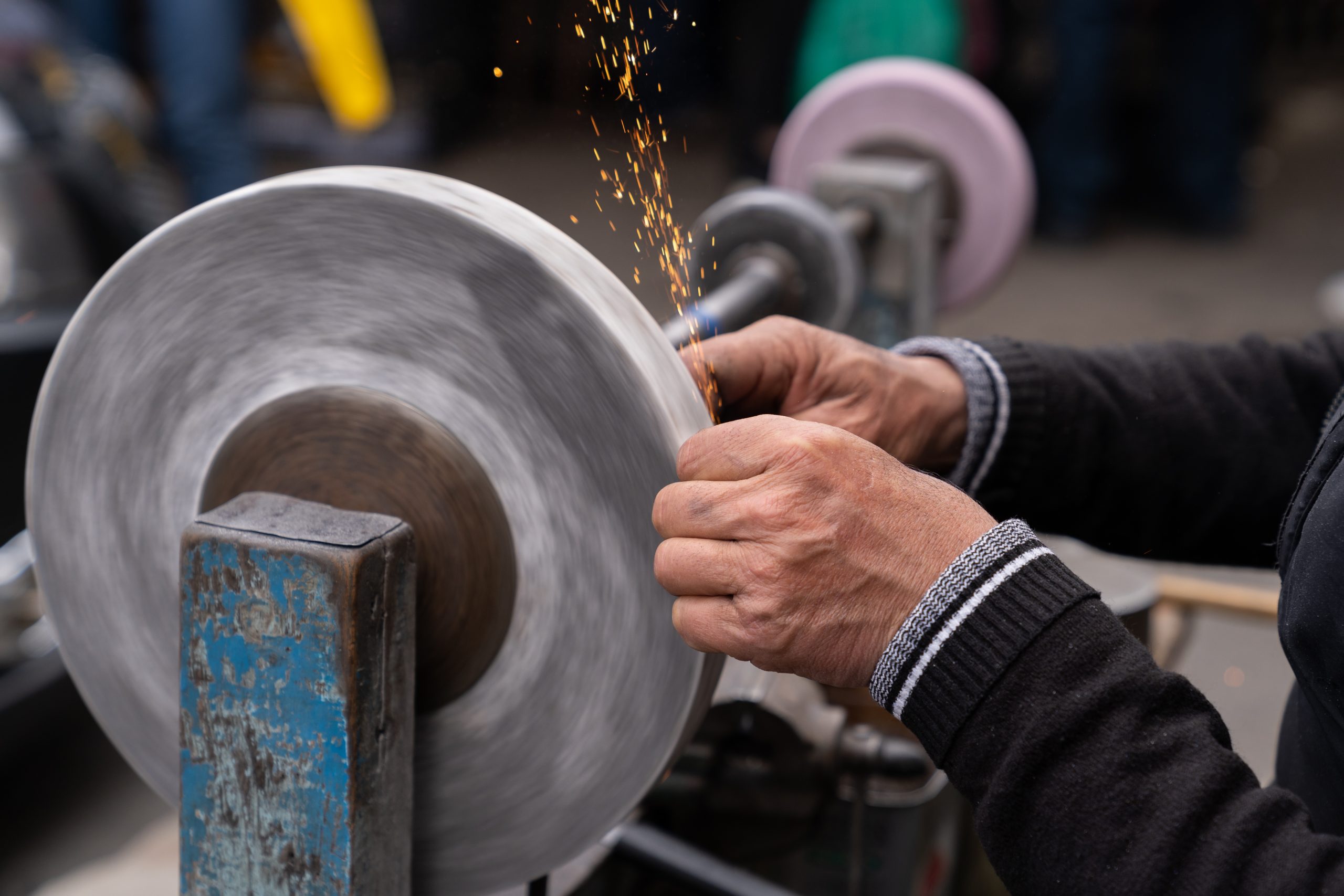
Comparing Metal Spinning to Other Metal Forming Techniques
Metal forming is a core process in modern manufacturing, turning raw materials into precisely engineered components. This process is essential in industries ranging from automotive and aerospace to construction and consumer goods. Metal forming techniques vary significantly, each offering unique efficiency, cost, and design flexibility advantages.
Among the many metal forming techniques available today, metal spinning stands out for its precision, efficiency, and cost-effectiveness. However, it is just one of several processes manufacturers can consider. Other popular methods include hydroforming, stamping, casting, rolling, and pressing, each of which has strengths and limitations.
This article explores how metal spinning compares to other prominent metal-forming techniques. By evaluating these processes, manufacturers can better understand the best approach for their specific production requirements.
Metal Spinning: A Versatile and Efficient Technique
Metal spinning is a specialist forming process that transforms a metal disc or tube into a symmetrical shape by rotating it at high speed and applying controlled pressure with a tool. This method is widely used in aerospace, lighting, and industrial manufacturing industries, where seamless, durable, and precise components are required. Metal spinning can be performed manually by skilled craftsmen or automated through CNC technology, ensuring repeatability and high precision.
Unlike other forming techniques, metal spinning is highly cost-effective, with low tooling costs and minimal material waste. The process strengthens the metal due to the work-hardening effect, making spun parts more durable than cast or stamped alternatives. Additionally, metal spinning allows for flexibility in modifying designs mid-production, reducing the risks and costs associated with retooling.
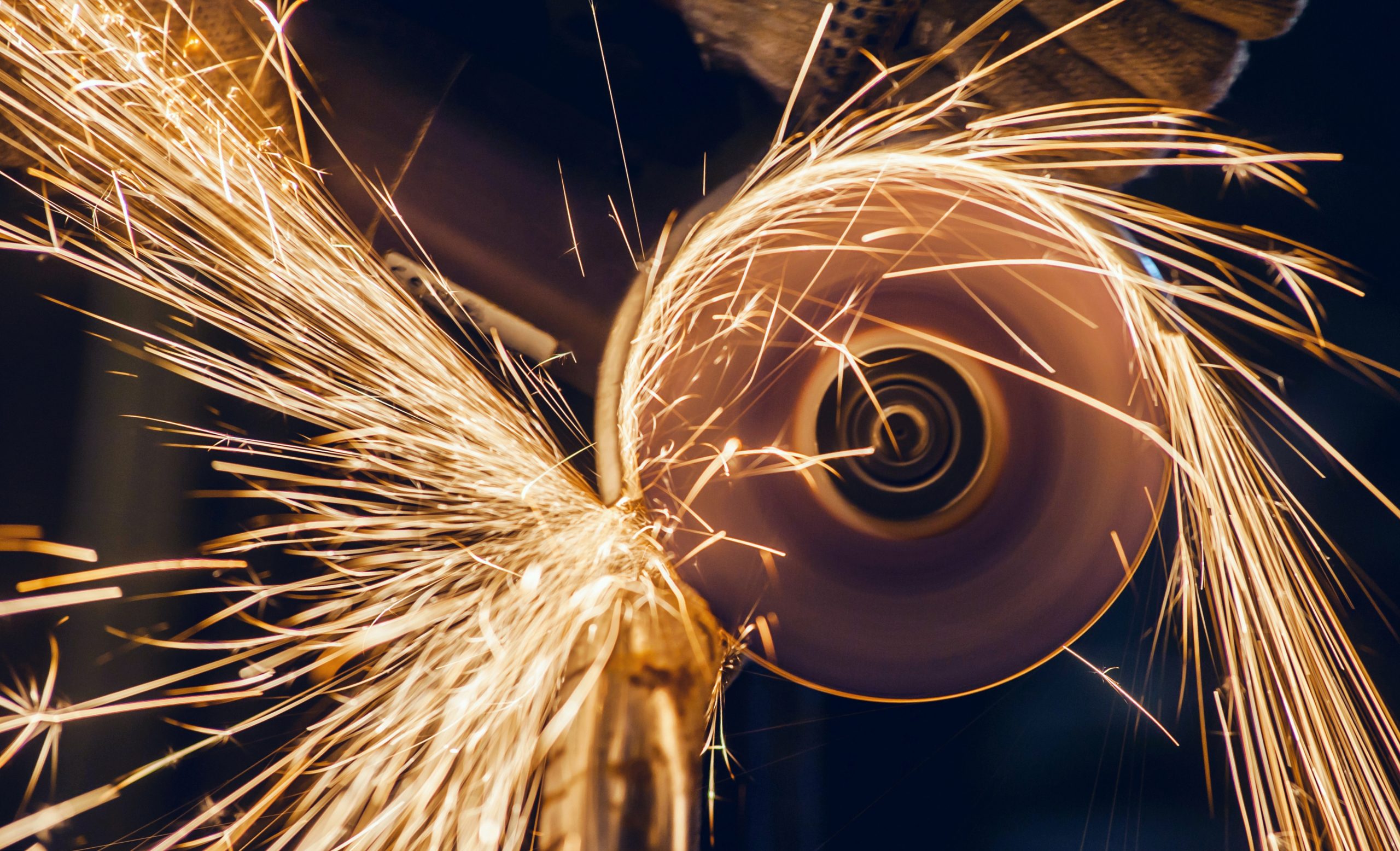
How Does Metal Spinning Compare to Other Forming Techniques?
Hydroforming: Strength in Complexity
Hydroforming uses high-pressure fluid to press metal sheets into complex shapes using a die. It is a common technique for forming lightweight yet strong components, particularly in the automotive and aerospace industries. Hydroforming enables the creation of intricate, asymmetrical geometries that would be difficult to achieve with metal spinning. However, the process involves higher tooling costs and longer cycle times, making it less suitable for smaller production runs.
Stamping: Speed and Precision for Mass Production
Stamping is a high-speed metal forming process that involves cutting, bending, and pressing metal sheets onto a die. This method is ideal for large-scale production of flat or shallow components with complex patterns. Stamping provides excellent precision and repeatability, making it a popular choice in the automotive and electronics industries.
However, the initial die creation cost is high, and design changes require costly retooling. Compared to metal spinning, stamping is less flexible for prototyping and short production runs. Additionally, while stamping is highly efficient for simple geometries, it struggles to accommodate more intricate or custom designs without extensive die modifications.
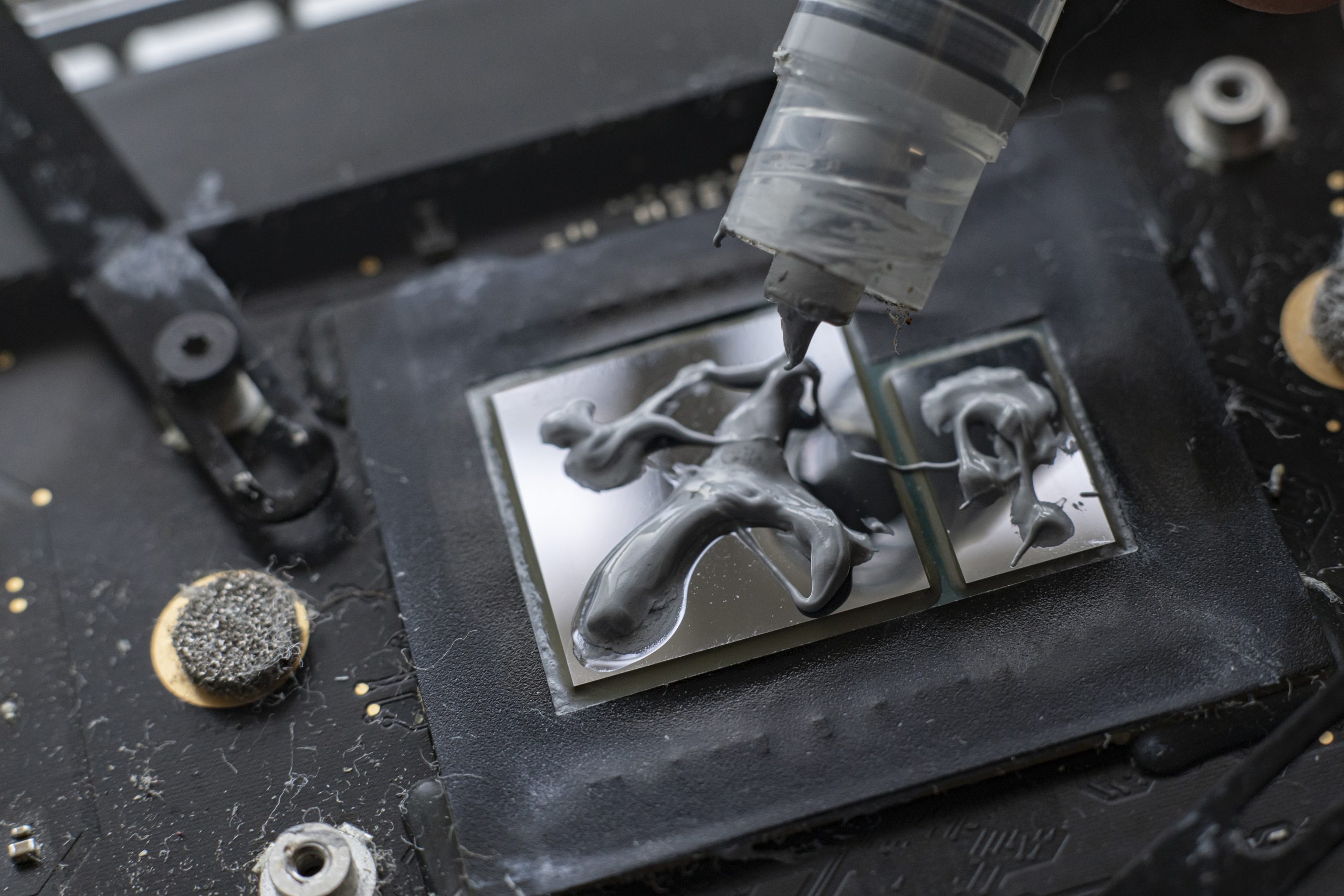
Casting: Ideal for Complex and Large-Scale Components
Casting involves pouring molten metal into a mould, allowing it to cool and solidify into the desired shape. It sees wide use in the production of large or intricately detailed components that may be challenging to manufacture using other forming methods. Casting is particularly beneficial for high-volume production but has drawbacks, such as the potential for porosity, longer production times, and higher energy consumption.
Unlike metal spinning, casting requires extensive finishing processes to achieve a smooth surface. Furthermore, cast components often need secondary machining to meet precise dimensional tolerances, which can extend lead times and increase costs.
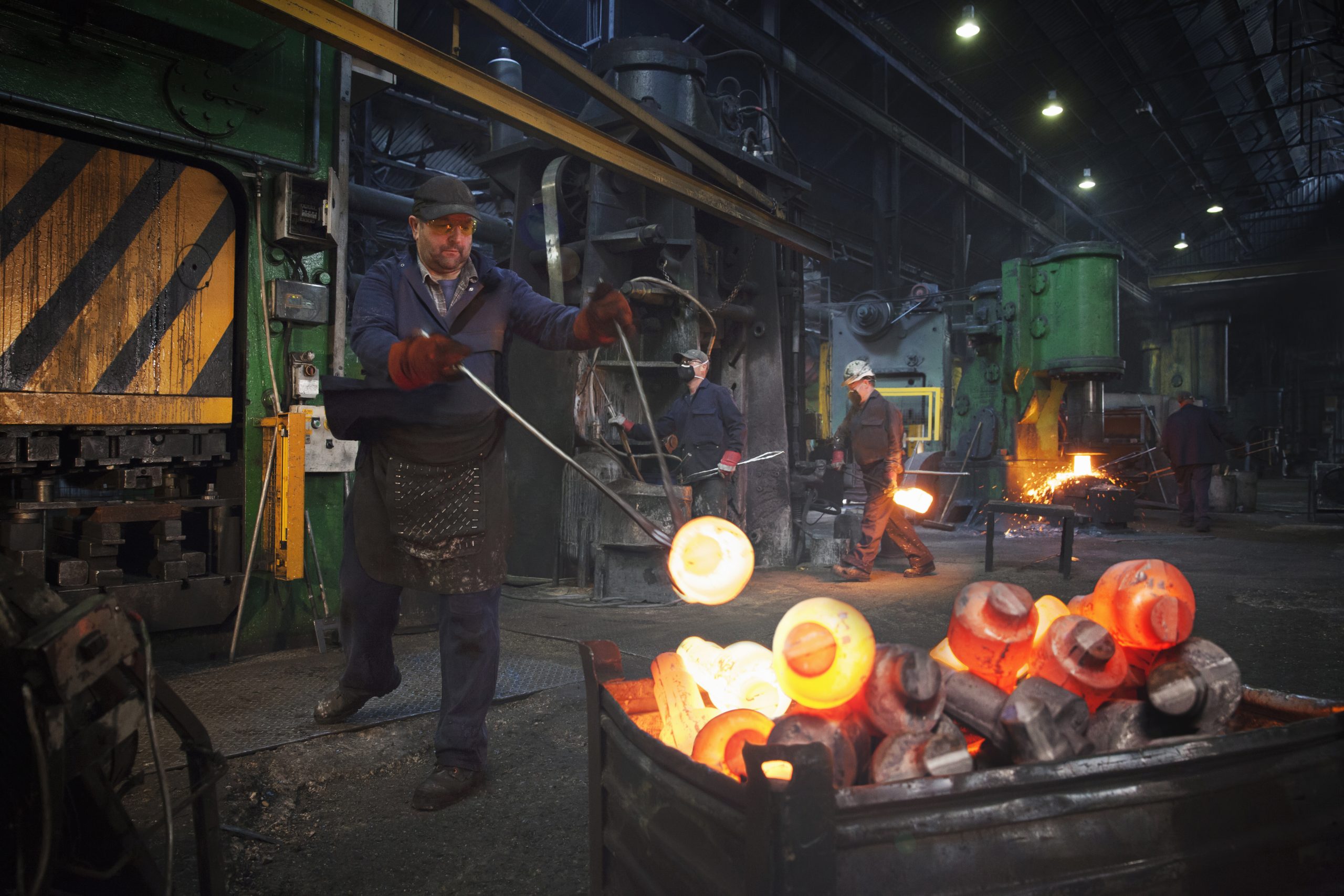
Rolling: Uniformity for Sheet Metal Applications
Rolling is a fundamental metal-forming process that reduces the thickness of metal sheets by passing them through rollers. This method is perfect for producing uniform sheets or preparing raw materials for further fabrication. While rolling is highly efficient for flattening metal, it is limited in the complexity of shapes it can achieve.
In contrast, metal spinning allows for the direct formation of final components without extensive secondary processing. Rolling also typically requires additional forming or machining steps to create final shapes, whereas metal spinning produces near-finished components in a single process.
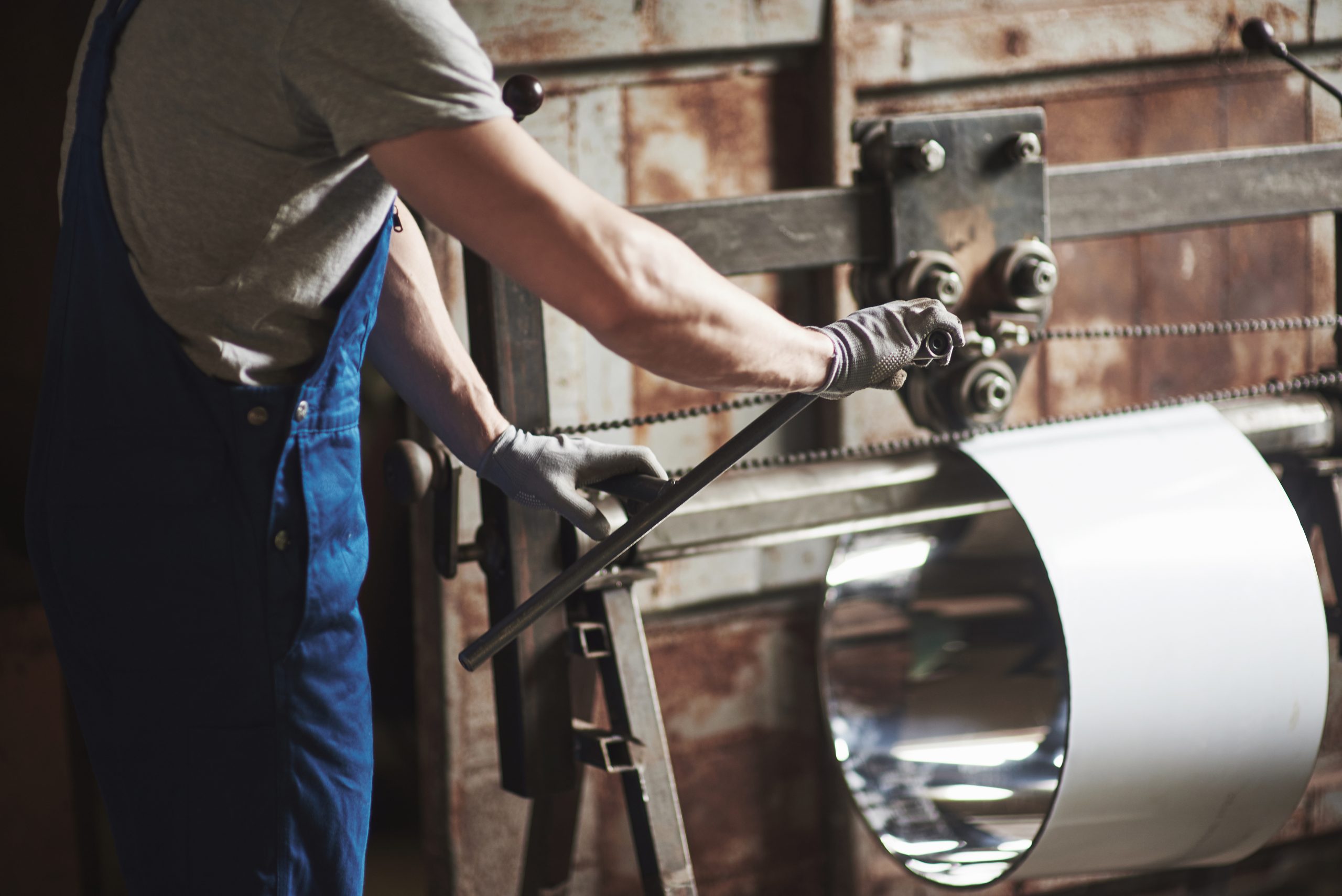
Pressing: A Flexible but Higher-Cost Alternative
Press forming involves shaping metal sheets or blanks using a hydraulic or mechanical press. This technique offers more flexibility than stamping, as it can create varied shapes, including cylinders and cones. Pressing is well-suited for large-scale production but may generate more material waste than metal spinning.
Additionally, tooling costs can be high, and adjustments to design specifications require significant modifications. While pressing can achieve high production speeds, it lacks the adaptability of metal spinning for low-to-medium volume runs, where frequent design changes may be necessary.
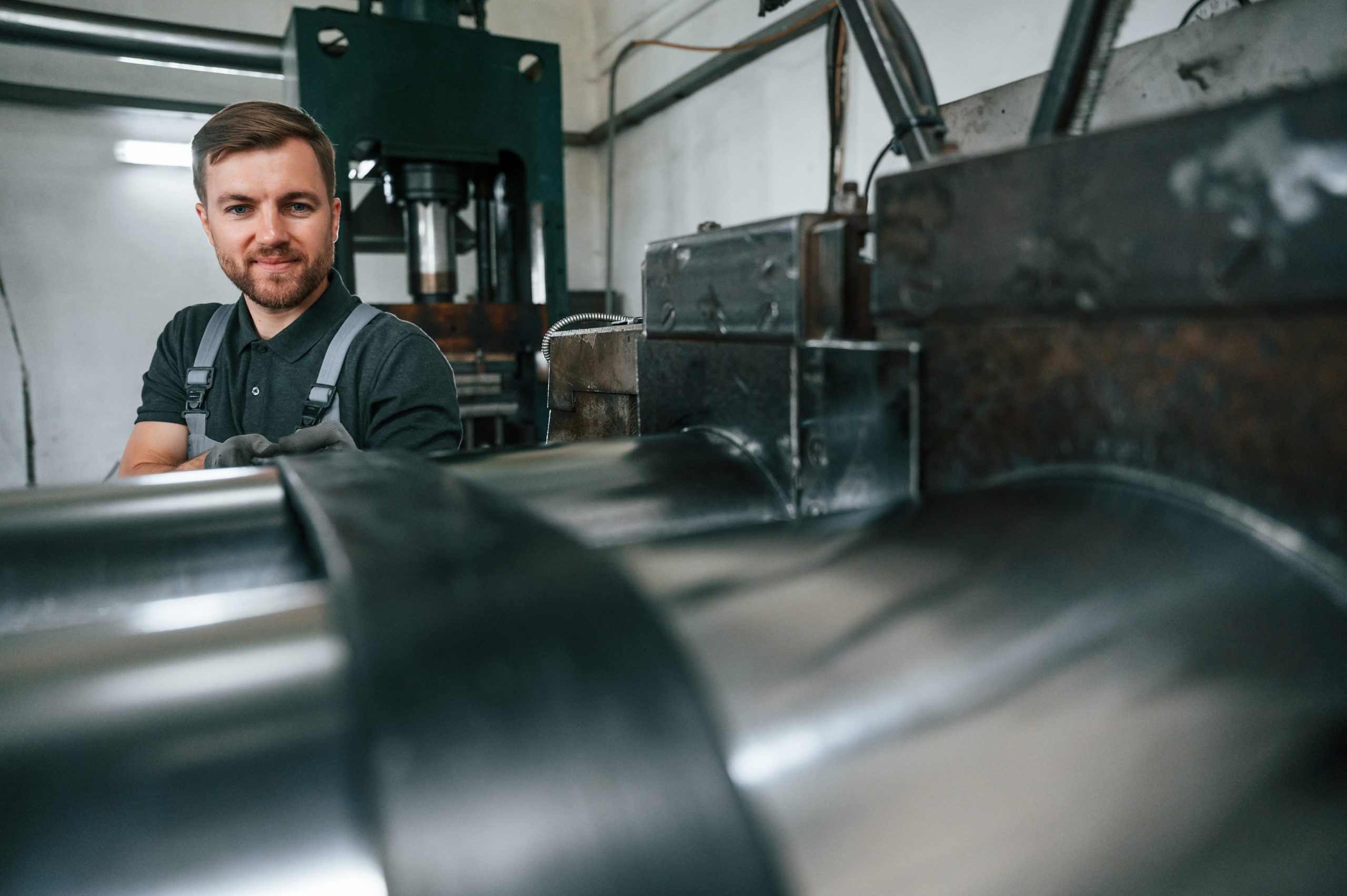
Why Choose Metal Spinning?
With so many metal forming techniques available, choosing the right one depends on factors such as the required production volume, material constraints, and design complexity. While other methods may be better suited for mass production or intricate, asymmetrical shapes, metal spinning provides a versatile and economical solution for a range of industries. Below are some key reasons manufacturers choose metal spinning over alternative forming techniques.
- Cost-Effective Tooling: Compared to stamping and casting, metal spinning requires minimal investment in tooling, making it a more affordable option for short to medium-production runs.
- Material Efficiency: The process generates less waste, optimises the use of raw materials, and reduces costs.
- Enhanced Strength: Unlike casting, which may introduce porosity, metal spinning strengthens the metal, improving its structural integrity.
- Flexibility and Adaptability: Spinning allows for adjustments during production without requiring entirely new tooling, unlike stamping or pressing.
- Scalability: With CNC automation, metal spinning achieves high precision and repeatability, making it competitive for larger production volumes.
- Seamless Parts: Unlike welding or assembling multiple pieces, metal spinning creates a single, seamless component, reducing weak points and improving structural durability.
- Energy Efficiency: Since metal spinning does not require the extreme heat levels of casting, it is often a more energy-efficient option, helping manufacturers reduce operational costs.
Limitations of Metal Spinning
While metal spinning offers numerous advantages, it is not without its limitations. It is essential for manufacturers to understand these constraints to determine whether this technique aligns with their specific production requirements. Below are some of the key challenges associated with metal spinning.
- Restricted to Symmetrical Shapes: The technique is most effective for producing cylindrical, conical, and dome-like structures, limiting its application for complex, non-symmetrical designs.
- Requires Skilled Operators: While CNC automation has improved consistency, traditional manual spinning relies on experienced technicians to achieve high-quality results.
- Moderate Production Speeds: Compared to stamping and casting, metal spinning may not be the fastest method for very high-volume production.
- Size Limitations: Although metal spinning can accommodate a range of sizes, manufacturing extremely large components may be more efficient using pressing or casting.
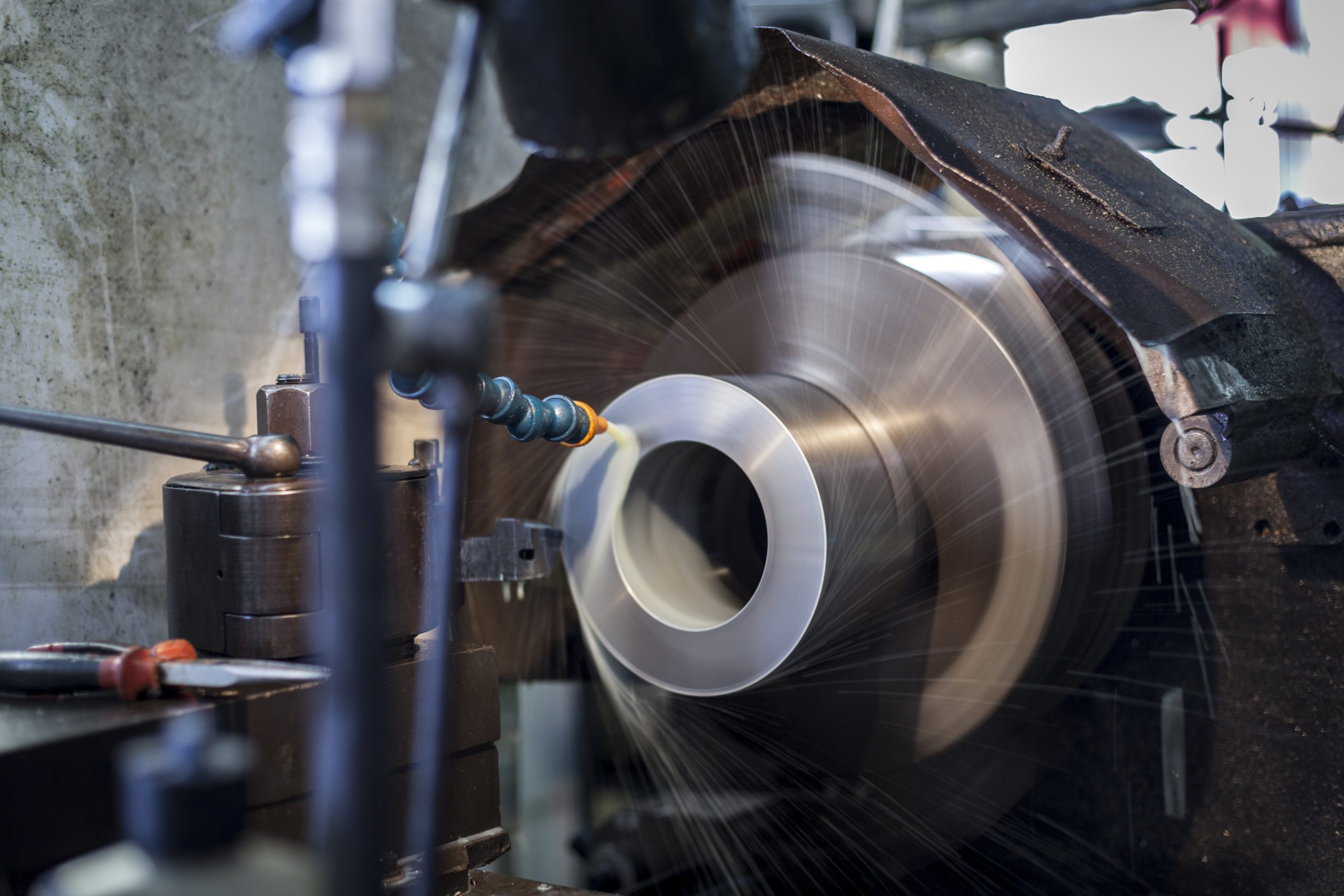
Selecting the Right Metal Forming Process
The ideal metal-forming technique depends on various factors, including production volume, part complexity, material properties, and cost considerations. Hydroforming and casting are excellent for intricate designs and large-scale production, while stamping is preferred for high-speed mass manufacturing. However, metal spinning offers an exceptional balance of affordability, precision, and efficiency, making it a versatile choice for manufacturers requiring seamless and durable components.
At Tanfield Metal Spinners, we provide expert metal spinning solutions tailored to meet the needs of various industries. Whether you require custom prototypes or large production runs, our extensive experience and advanced CNC capabilities ensure the highest quality standards. Contact us today to explore how metal spinning can optimise your manufacturing process.